MoComp Bogies
Siemens Mobility at Graz Eggenberg site stands for decades of experience in development and production of bogies and pantographs. Cooperation with universities, application of innovative technologies guarantee sustainable quality of MoComp bogies. The integration of Customer Service ensures bundled competence along the entire life cycle of our products.
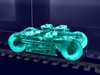
Siemens Mobility at Graz Eggenberg site stands for decades of experience in development and production of bogies and pantographs. Cooperation with universities, application of innovative technologies guarantee sustainable quality of MoComp bogies. The integration of Customer Service ensures bundled competence along the entire life cycle of our products.