Spare parts – 3D printing for railways
Reduction of CO₂ emissions by more than 10% through additive manufacturing. More than 110 customers – more than 2,100 different parts in our virtual stock – more than 31,000 printed and sold customer parts and far more 3D printed solutions for our maintenance and production facilities, such as production aids, templates, or fixtures.
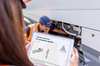
Reduction of CO₂ emissions by more than 10% through additive manufacturing. More than 110 customers – more than 2,100 different parts in our virtual stock – more than 31,000 printed and sold customer parts and far more 3D printed solutions for our maintenance and production facilities, such as production aids, templates, or fixtures.